Battery charger in substation
Home / Energy Power / Substation Battery Market
Substation Battery Market Size, Share Industry Analysis, By Type (Nickel Cadmium Battery, Lead Acid Battery, Others), By Application (Residential Commercial, Industrial, Utilities) and Regional Forecast, 2023-2030
An uninterrupted power supply is essential for a higher level of productivity to avoid losses. Frequent power outage or unreliable power supply causes overall performance of the company and hampers the productivity incurred in major losses. The industries and commercial buildings constructing their own substation with the help of batteries to avoid power outage. Substation battery ensures that all the electrical equipment in a substation continue to operate in the event of a power outage.
The DC system is vital component of a high voltage industrial or utility substation. It supplies energy needed to manage the protective devices and high voltage component and allows electrical faults to be safely isolated. Therefore, in many industrial and commercial application substation batteries are deployed to enhance the reliability of power supply and avoid power outage.
The substation battery market is segmented into type and application. Types are further divided into the lead-acid battery, nickel-cadmium battery, and others. The lead-acid battery is extensively used for in substation owing to its highly reliable performance and matured technology. Industrial and commercial sector accounts the major market of substation battery due to demand for uninterrupted power supply.
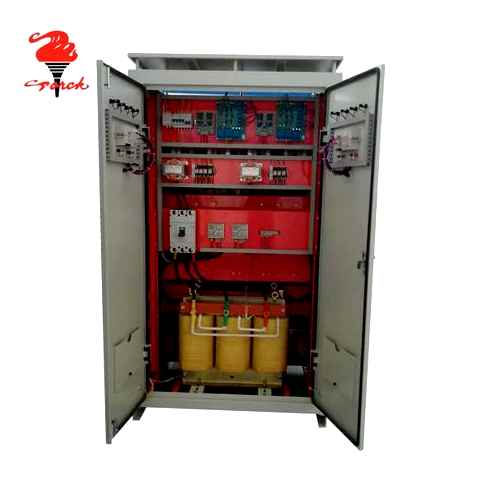
Steadily rising demand for uninterrupted power supply from industries and commercial spaces to avoid power losses in order to enhance productivity is boosting the growth of the substation battery market. Many countries across the globe embracing e-mobility for public transportation and promoting e-vehicle along with building battery charging station infrastructure is expected to drive the substation battery market.
Generators are flexible with a wide range of high voltage application, and they are highly reliable as compared to substation battery. Also performance of the battery degrades over the years which negatively impacts the longevity of the battery which limits the growth of the substation battery market.
Key Players Covered
The major substation battery companies are Exide Technologies, GS Yuasa International Ltd., Saft, Robert Bosch GmbH, Johnson Controls, Amara Raja Group, EnerSys, Luminous Power Technologies (P) Ltd, Trojan Battery Company, Exide Industries, SolarEdge Technologies, Tesla, HBL Power Systems Ltd.
By Application
By Geography
- North America (the USA and Canada)
- Europe (UK, Germany, France, Italy, Spain, Russia and Rest of Europe)
- Asia Pacific (Japan, China, India, Australia, Southeast Asia and Rest of Asia Pacific)
- Latin America (Brazil, Mexico and Rest of Latin America)
- Middle East and Africa (South Africa, GCC and Rest of Middle East and Africa)
Regional Analysis
The substation battery market is segmented into North America, Europe, Asia Pacific, Latin America, and the Middle East and Africa. Technological development augmented the growth of the substation battery market in North America. Deployment of batteries in large scale companies to avoid power failure and rising demand for uninterrupted power supply is supposed to enlarge the growth of the substation battery market in North America. Europe is adapting e-mobility for public transportation and promoting e-vehicle to mitigate the rising GHG emission. Auto companies along with government assistance building charging station for e-vehicle is expected to leverage the demand for substation battery market in Europe. The Asia Pacific is dominating the substation battery market owing to rising industrialization and commercialization which needs an uninterrupted power supply to enhance productivity. The steadily rising economy of China and India is also contributing to the growth of the substation battery market. The substation battery market in MEA is expected to grow at steady rate due to lack of infrastructure, low-level income, limited industrial scope which inhibits the growth opportunities.
- In August 2019, Indian Oil plans to build a 1GW electric vehicle battery plant with a globally acclaimed start-up company. The move will assist in government vision of green mobility and facilitate the adoption of EV’s in the country.
- In October 2018, SolarEdge acquired 75% share of South Korean battery manufacturer company Kokam for 88 million and intended to buy remaining stakes in future.
- In August 2018, Exide Industries and Furukawa battery have signed an agreement to build ultra-battery and sell it to Indian automotive sector. Furukawa will provide technical assistance to Exide in the manufacturing ultra-battery.
Gzdw DC Power Distribution Supply Panel / Substation Battery Charger Panel Controller Cabinet
Our perfect management system and rich production experience make our JDCF voltage transformer, 108KV Porcelain JAcket Arrester, VS1 have excellent quality. In today’s globalization, we need further establish the concept of open development in order to build an ambitious, responsible, and respected enterprise. Adhering to the tenet of faithful, professional and enthusiastic service, we will expand more sales channels, expand market share and grasp potential business opportunities.
GZDW DC Power Switchgear can be used in the DC power supply required by metallurgy, railway, mining, petrochemical, post and telecommunications, medical and health, banks, hotels, high-rise buildings and computer networks; the microcomputer-controlled DC power supply cabinet can be used for unattended, remote centralized monitoring DC power supplies in power plants, substations and other industries.
This product is loaded with the standard of JB/T5777 4-2000 General Technical Conditions and Safety Requirements for DC Power Supply Equipment in Power Systems.
FAQ:
Q1. Are you a factory or trading company?
Q2.Can I order a GZDW DC Power Switchgear sample?
A2:Yes, we accept any sample orders.
Q3: Could I have of your products?
A3: Welcome. Please feel free to send us an inquiry here. We will reply you within 24 hours.
Our company adheres to the core values of quality first and service winning, and is willing to work closely with colleagues and customers all over the world to promote the development of the Gzdw DC Power Distribution Supply Panel / Substation Battery Charger Panel Controller Cabinet industry. The whole production process of our company, from the purchase of raw materials, incoming inspection, process control, finished product inspection to product delivery, and even after-sales service, is strictly controlled in accordance with the relevant provisions of the quality assurance system. To increase the quality of our products and services, we FOCUS on technological innovation and follow the idea of creating value for customers.
Why you may need an industrial battery charger upgrade
Critical power upgrades, for assets including but not limited to industrial battery chargers, happen for a variety of reasons. These issues can sneak up on companies, as the backup system may not even be noticed until it is needed. Of course, by that point, if there is a fault in the system, it will be too late to do anything about it.
Some of the leading causes of critical power issues, things that may be revealed in the course of a power assessment, include the following:
- A failure of installation, documentation or maintenance: Some systems are in place for so long that their origins are forgotten or poorly documented. This infrastructure can stay in place for years because it isn’t broken, but if it is tested by a power failure, the weaknesses will become apparent. Rather than finding out about a poorly installed or maintained industrial battery charger in a moment of crisis, it pays to assess the existing system as soon as possible.
- Aging batteries and related equipment: As parts of your mission-critical backup power infrastructure start to age, it may become more expensive to repair them and replace them piece by piece than to update to a modern model. The added advantage of such a replacement is that you gain access to the latest features on your new industrial battery charger, ranging from improved interfaces to reliability upgrades and more.
- Need for consistency: If you want to ensure your entire critical power infrastructure is consistent, from the battery cells themselves to the chargers and beyond, you can replace your present system with a new, optimized version. Whether you opt to run the battery management functions in-house or select a power-as-a-service model, working with a single partner organization can clarify everything from tech specs to billing.
- Clarity around ownership, accountability and total cost of ownership (TCO): In addition to giving you a fresh start from a technical perspective, upgrading your battery charging and related hardware also provides a good opportunity to revise best practices around everyday procedures, safety and more. You can also gain insights into the exact costs involved, then track them for the devices’ whole usable life span. Whether you keep the responsibility among your team or turn to outside contractors, the change can be a positive one.
These motivating factors and more apply across industries and facility types. As long as you operate an industrial battery backup system, there is a need to check in and make sure every variable is being maximized, from battery life to reliability and beyond.
This need for technical soundness comes along with budgetary considerations. Your critical power infrastructure is essential to supporting your mission, so it can’t be removed from the budget. With the right approach to keeping all relevant systems up to date, however, you can optimize spend in this area.
How optimized battery charging helps across sectors
An industrial battery charger is an essential part of the equipment lineup across all companies that use backup power. This includes some of the highest-pressure essential functions, from health care to utilities and other parts of the energy ecosystem.
Battery backup is also essential in data center settings, keeping customer data, important records and more safe. The emerging lithium ion battery backup option has become especially popular in these data centers, ensuring uptime with these high-efficiency cells.
Specific industries in need of reliable industrial battery charging solutions as part of their backup power infrastructure include:
- Telecommunications and cable providers: In the telecom space, you need to ensure there are fully charged battery backups available at multiple points. From central and remote offices to outdoor cabinets attached to substations, critical power solutions are a mission-critical consideration.
- Health care: In medical settings such as hospitals and clinics, the presence of a reliable battery backup solution can literally prove lifesaving. The battery room at a health care facility should be equipped with the latest and highest-tech solutions spanning industrial battery charging, monitoring and more.
- Power generation facilities and utilities: At a generation site such as a dam or power plant, the stakes for battery backup solutions are high. In general, the utility sector must be able to count on its critical power technology to make sure it can FOCUS on remediating issues when they arise.
- Financial institutions: Safeguarding the integrity of the important and fast-moving data stored in financial institutions’ high-powered data centers is a high priority for these organizations. Without a dependable way to ensure battery backups are charged to proper levels and ready for use, these companies are missing a key piece of redundancy.
- Data centers: Large companies that run their own mission-critical data centers should be thinking about their critical power performance. The same goes for colocation and Cloud provider data centers, with essential information belonging to numerous owners residing in their servers. These data centers’ battery rooms must have the latest equipment to inspire confidence in tenants.
In general, organizations with critical power needs that are pressing enough to warrant the creation of dedicated battery rooms must ensure these spaces are equipped with assets that will provide both safe operations and reliable power generation when called upon.
Industrial battery charging systems equipped with sensors and alarms to detect under- and overcharging are part of this safety-first design mindset. These can be paired with devices such as spill containment systems and acid-resistant floors when using flooded lead acid batteries.
The spaces should also be designed in a careful and intentional way — for instance, the placement of battery storage racks is an important consideration. Furthermore, they should be kept at a standard temperature and well ventilated. Your employees should always feel safe when servicing the equipment, and though modern industrial battery chargers can survive in extreme environmental conditions, they shouldn’t have to do so.
In the case of a power loss, your company needs to be able to count on its battery backup system, whether it is stationed in a battery room or a remote enclosure. As with design and installation, one way to gain confidence in the everyday operations of your critical power system is to purchase it as part of a power-as-a-service contract.
Power as a service and industrial battery charging
While the standard approach to maintaining industrial battery charging. maintenance and upkeep involves assigning an internal team of employees to the task, there is another way. After assessing your backup critical power needs, you have a choice: Will you build and maintain the new infrastructure in house, or select a power-as-a-service offering?
Using a managed service model is a way to make sure all necessary functions are taken care of by experts, without the need for hiring, retraining and upskilling. This approach also avoids the capital expenses associated with purchasing hardware in favor of a predictable monthly operating expense model.
The ongoing management of battery rooms and other critical power installations will have to be part of your organization’s budget in one way or another. By deciding whether the upkeep is best handled by an internal or third-party team, you can take control of the nature of the spending and management. Managed service teams work to optimize the performance of systems, using their industry knowledge to ensure your backup system is ready when you need it most.
Substation battery sizing calculation
Now, let’s do some math and size a flooded cell, lead-acid battery for a substation. The battery will be rated 125V DC nominal and have an amp-hour capacity rated for an 8-hour rate of discharge.
In most substations, the 8-hour rate of discharge is the standard. It gives operators a solid 8-hour window to sort out any AC power supply issues before everything goes haywire.
Important Note: We’ll be using the IEEE Standard 485 for our substation battery sizing calculation. This standard helps us define DC loads and size lead-acid batteries.
But first, let’s quickly go over the two types of loads in a substation:
- Continuous loads usually run for 8-hour periods.
- Momentary loads only operate for less than a minute.
With that out of the way, let’s jump into the loads for our substation battery sizing calculation.
Continuous load list
- Auxiliary relays timers: (10) x 5VA = 50VA
- Indicating lights (LED): (20) x 5.5VA = 110VA
- Multifunction relays: (18) x 5VA = 90VA
- Power meter: (16) x 10VA = 160VA
- SCADA allowance: 1000VA
Total: 50VA 110VA 90VA 160VA 1000VA = 1,410VA
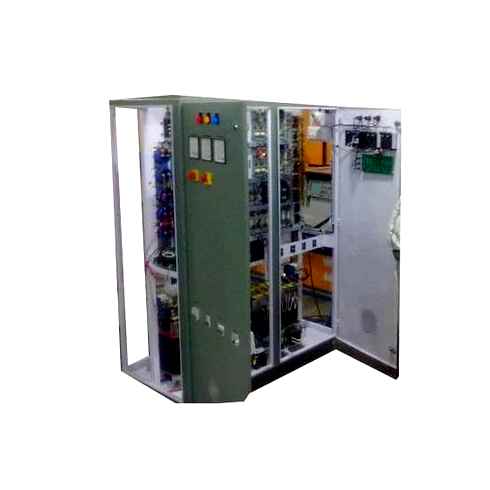
Important Note: “Multifunction relays” include all your regular protection relays like 86L, 86B, 86T, 151T/151N, 87A, 51AT, and so on. We’ll group them together to make things simpler in our calculation.
Each relay usually has a load no greater than 5VA, but make sure to double-check each relay’s load individually.
Intermittent load list
- Auxiliary relays: (5) x 5VA = 25VA at 1 second
- Breaker close coil: (20) x 150VA = 3,000VA at 0.05 seconds
- Breaker spring winding motor: (20) x 500VA = 10,000VA at 5 seconds
- Lockout relays: (6) x 325VA = 1,950VA at 0.01 seconds
- Breaker trip coil: (20) x 150VA = 3,000VA at 0.03 seconds
Total summed design load
Peak load ( ) = Continuous load Intermittent load
Important Note: Sometimes, both the ‘main breaker trip coil’ and ‘breaker close coil’ aren’t factored into the peak load calculation. Take, for instance, a generator breaker at a hydroelectric facility. When a trip occurs, it usually hints at a more significant problem requiring further investigation by an operator before closing the breaker.
In a hydro facility, backfeeding into the power system can be risky business, so we need to tread carefully. As a result, a situation where a breaker trips and closes immediately just doesn’t happen too often. To prevent overestimating the load, we include only the trip or close coil in our calculations.
Design load. where:
- = contingency for future load growth (assume 10% = 0.1)
- = design contingency margin (assume 10% = 0.1)
Important battery notes
1) Heavy discharge: Lead-acid batteries prefer intermittent loads over continuous loads. Intermittent loads give batteries a rest period to recompose their chemical reaction.
2) Battery room ventilation: Lead-acid batteries release hydrogen gas when recharging. Without proper ventilation, hydrogen gas builds up and increases explosion risks.
3) Battery room temperature: The optimum temperature for lead-acid batteries is normally between 68-77° Fahrenheit. If the temperature goes too much higher, battery life will shorten.
4) Slow charging: Lead-acid batteries charge slowly. The typical charging time is 14 to 16 hours.
5) Full state of charge: Lead-acid batteries need to always remain fully charged. A low charge causes sulfation, leading to attenuated performance.

6) Charging voltage: To maintain optimal battery performance, it’s important to use the correct charging voltage limits. A low voltage limit can cause poor battery performance and sulfation buildup on the negative battery plate. On the other hand, a high voltage limit can improve performance, but it can also cause grid corrosion to form on the positive battery plate.
It’s super important that your battery charger applies the appropriate voltage to a fully charged battery. This way, you’ll avoid overcharging and any potential damage.
Substation battery sizing calculation wrap up
Sizing your substation’s batteries doesn’t have to be a headache. Just gather your load info (okay, that part might be a bit tedious) and you’re all set.
Think of a power substation like a massive machine. Like any machine, it needs backup plans for its critical components. Redundancy is key! So, make sure to include the right-sized batteries and chargers in your substation setup to avoid costly downtimes.
Do you have any substation battery sizing tips? Where else have you seen batteries providing backup to the main power source?